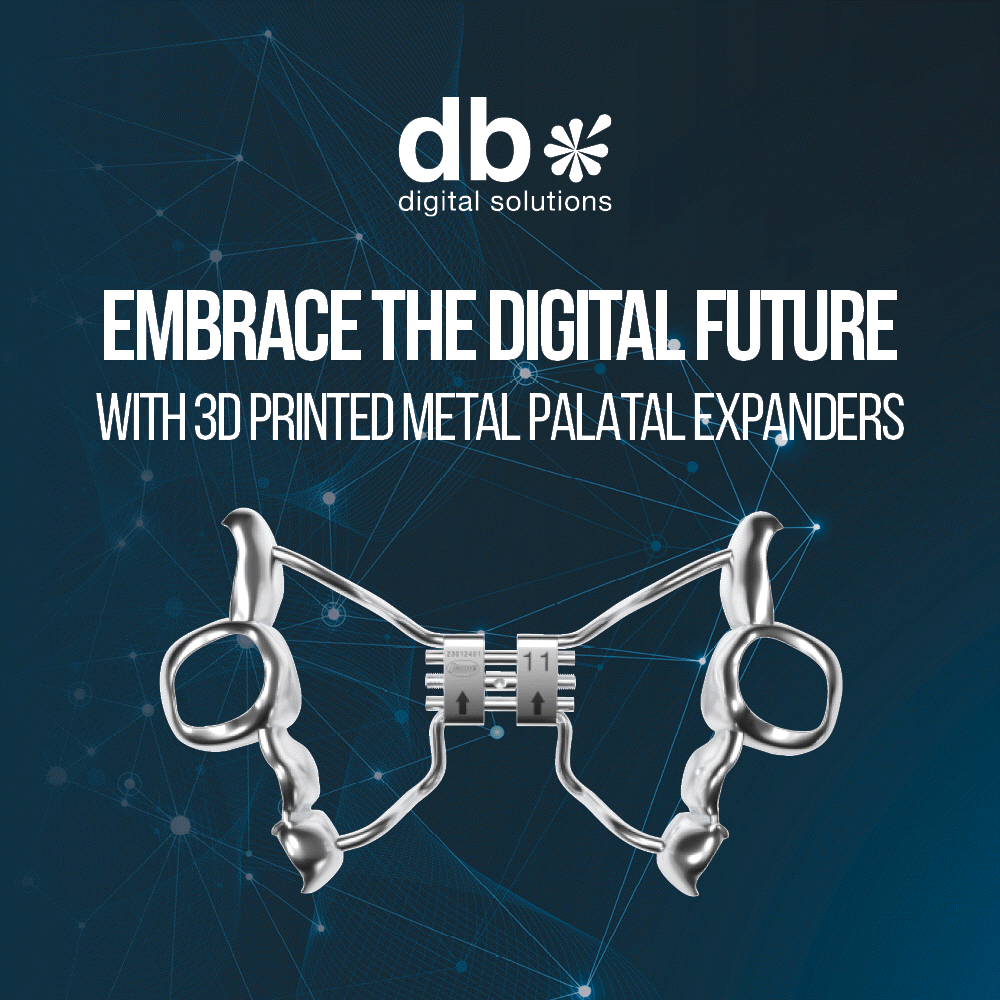
This IDS, 3D Printed Metal Palatal Expanders, also known as Rapid Maxillary Expanders (RME) from DB Digital Solutions are a "must-see" innovation for 2025. Visit stand G018, Hall 4.2 to see the accuracy and precision featured in each appliance. Here are some of your most asked questions about the RME, Leaf RME, and TAD based / MARPE appliances.
1. What are the benefits of 3D Metal Printed RMEs?
These cutting-edge appliances remove the need for molar bands; reducing the number of appointments and chair time, and make the process more comfortable for the patient as separators are also no longer required. The orthodontist benefits from the certainty of an easy-to-fit precision appliance due to the precise nature and full customisation of the 3D design and printing process.
2. How do I send scans?
We are compatible with platforms including iTero, 3Shape, Dentsply Sirona and Medit. Additionally, we accept scans via email attachment, WeTransfer and Dropbox.
3. How do I order an RME and submit specifications?
Send an upper stl file, upper impression or model, along with our prescription form which can be found online at https://www.dbdigitalsolutions.co.uk/forms
We can accommodate a wide variety of different case customisation so please indicate on your prescription form any specific design requirements, including the addition of buccal tubes if required. If you have any questions, don’t hesitate to give us a call. Being based here in the UK we are easily accessible and always happy to help.
4. What is the workflow?
After sending your scan/impression or model you will be informed that we have received your case. For RME cases we can share the design with you prior to print via a link to the viewer software where the design can be reviewed (the more familiar you become with the process you may wish to omit this step). Once approved the appliance will be ready to ship within 5 working days and we will inform you of the despatch day.
To learn more visit dbdigitalsolutions.co.uk.
1. What are the benefits of 3D Metal Printed RMEs?
These cutting-edge appliances remove the need for molar bands; reducing the number of appointments and chair time, and make the process more comfortable for the patient as separators are also no longer required. The orthodontist benefits from the certainty of an easy-to-fit precision appliance due to the precise nature and full customisation of the 3D design and printing process.
2. How do I send scans?
We are compatible with platforms including iTero, 3Shape, Dentsply Sirona and Medit. Additionally, we accept scans via email attachment, WeTransfer and Dropbox.
3. How do I order an RME and submit specifications?
Send an upper stl file, upper impression or model, along with our prescription form which can be found online at https://www.dbdigitalsolutions.co.uk/forms
We can accommodate a wide variety of different case customisation so please indicate on your prescription form any specific design requirements, including the addition of buccal tubes if required. If you have any questions, don’t hesitate to give us a call. Being based here in the UK we are easily accessible and always happy to help.
4. What is the workflow?
After sending your scan/impression or model you will be informed that we have received your case. For RME cases we can share the design with you prior to print via a link to the viewer software where the design can be reviewed (the more familiar you become with the process you may wish to omit this step). Once approved the appliance will be ready to ship within 5 working days and we will inform you of the despatch day.
To learn more visit dbdigitalsolutions.co.uk.
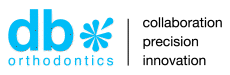
Unit 6 Ryefield Way
KEIGHLEY BD20 0EF
Großbritannien
KEIGHLEY BD20 0EF
Großbritannien
Halle 4.2 | G018